材料の無駄を最小限に抑えるボトル自動組立機の効率は、設計、精度、制御機構などのいくつかの要因によって異なります。この点で効率に影響を与える可能性がある考慮事項をいくつか示します。
精密エンジニアリング: 精密エンジニアリングの分野では、ボトル組立機のすべてのコンポーネントが、最大限の精度と一貫性で動作するように細心の注意を払って設計および作成されています。これには、CNC 加工、レーザー切断、EDM (放電加工) などの高度な製造技術を採用して、すべての部品が厳しい公差を満たすようにすることが含まれます。たとえば、射出成形プロセスで使用される金型は、製造されるボトルの形状と寸法の均一性を保証するために、ミクロレベルの精度で設計されています。これらのコンポーネントの構築に使用される材料は、耐久性、熱安定性、耐摩耗性を考慮して慎重に選択されており、これにより機械の寿命と信頼性が向上します。
最適化された生産パラメータ: 生産パラメータの最適化について話すとき、私たちは、ほんのわずかな調整が効率と無駄の削減に大きな影響を与える可能性がある領域を掘り下げています。たとえば、プラスチック ボトルの製造の場合、射出圧力、金型温度、冷却速度、サイクル タイムなどの要素が細心の注意を払って調整され、速度と品質の完璧なバランスが実現されます。高度なソフトウェア アルゴリズムを使用して、機械に組み込まれたセンサーからのリアルタイム データを分析することができ、オペレーターが最適なパフォーマンスを得るためにこれらのパラメーターをオンザフライで微調整できるようになります。このレベルの精度は、材料の無駄を最小限に抑えるだけでなく、製品の一貫性を高め、欠陥の可能性を減らします。
統合された品質管理: 組立ラインから出てくるすべてのボトルが、流通に適していると判断される前に一連の厳格なテストと検査を受けるシナリオを想像してください。まさにそれが、統合された品質管理メカニズムによって可能になります。これらの機械は、最先端のセンサー、カメラ、視覚システムを利用して、気泡、表面の凹凸、寸法のばらつきなどの欠陥がないか各ボトルを精査します。指定された品質基準から逸脱すると、ただちにアラートが発せられ、オペレーターが介入して根本的な問題を修正するよう促されます。これらのシステムは、潜在的な欠陥を芽のうちに摘み取ることで、材料の無駄を最小限に抑えるだけでなく、完璧な製品を提供するというブランドの評判を維持します。
マテリアル ハンドリング システム: マテリアル ハンドリング システムは、効率的な組み立て作業のバックボーンを形成し、原材料のシームレスなフローと利用を保証するサイレント オーケストレーターとして機能します。ロボット アーム、コンベア ベルト、自動フィーダーが完璧に調和して動作し、適切な量の材料を組立ラインの各ステーションに正確に供給している様子を想像してください。これらのシステムは、流出や汚染を最小限に抑えるだけでなく、不必要な取り扱いや移送の手順を排除することで材料の使用を最適化するように設計されています。高度な分別とリサイクルのメカニズムにより、スクラップ材料を再処理または再利用のために分別することで効率がさらに向上し、廃棄物発生のループを閉じます。
モジュラー デザイン: モジュラー デザインの概念は、レゴ ブロックで遊ぶのに似ており、コンポーネントを自由に組み合わせて事実上無限の構成を作成できます。ボトル組立機械の文脈では、モジュール性は柔軟性、つまり変化する生産要件や市場の需要に応じて適応し進化する能力に変換されます。機械は、いくつかの簡単な調整を行うだけで、500 ml ペットボトルの製造から 1 リットルのガラスボトルの製造にシームレスに移行できます。この多用途性により、ダウンタイムが最小限に抑えられるだけでなく、工具の変更やセットアップ手順に伴う材料の無駄も削減されます。モジュラー設計によりメンテナンスとアップグレードが容易になり、マシンがライフサイクル全体を通じて最先端のテクノロジーを維持できるようになります。
ボトル自動組立機
ボトル自動組立機
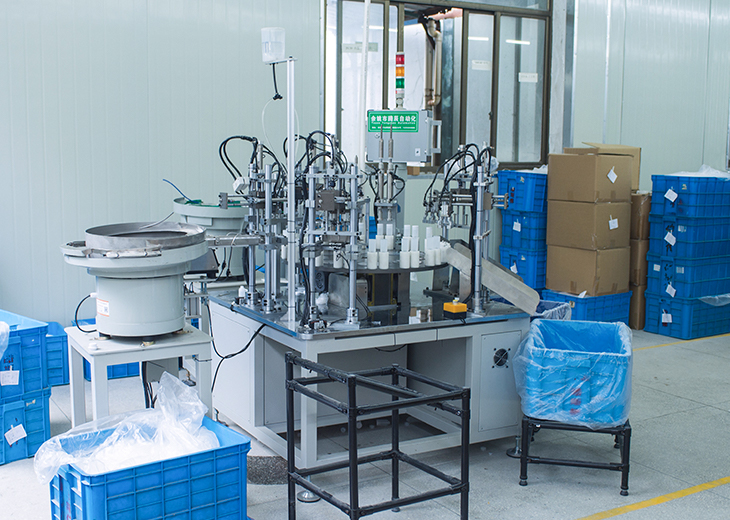